1.製造のポイント
当社の人形師は、本練り技法を継承している金沢で唯一の職人です。 『本練り』とは、江戸時代から続く技法の一つです。 桐の大鋸屑を麩糊で固め、胡粉(ごふん=ハマグリ・カキ貝から作られる粉)を膠(にかわ=動物の皮や骨等から作られる接着剤)で溶かし、何回も塗り上げる技法です。
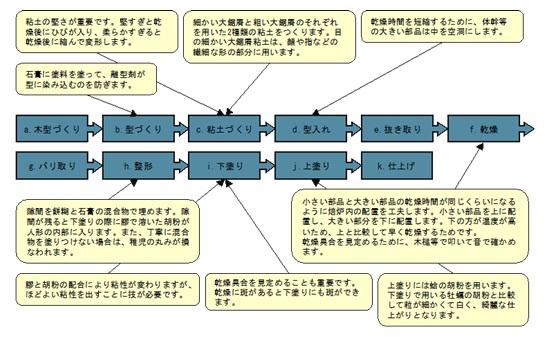
※上の図をクリックすると拡大表示します。
2.製造工程の詳細
ここでは、加賀人形の製造工程を詳しく説明します。
(1)木型づくり
加賀人形は木型づくりからはじまります。 木型は原木を削って造ります。 稚児の体の丸みをだすためには一定程度の技が必要です。
(2)型づくり
粘土状にした石膏を木型に押し付けて型を取ります。 型を取った石膏を型木にはめます。 石膏には塗料が塗られていますが、これは離型材が石膏や型木に染み込まないようにするためです。
(3)粘土づくり
石川県産の桐の大鋸屑と麩糊を混ぜて炊きます。 桐は灰汁が出ないため粘土づくりに適しています。 鶴来産の桐は上質であることで有名です。
粘土づくりには以下の二つの技が活きています。
●粘土の堅さを調節する
●大鋸屑の粗さにより粘土を2種類つくる
(4)型入れ
型に離型材を塗ってから、適当な硬さになった粘土を詰めます。 成型物が体幹など大きいものの場合は、中が空洞になるように摺り子木等で押しつけてほじります。
(5)抜き取り
型を閉じて密着させて成型した後に型から成型物を抜き取ります。 抜き取る際に形が大きく変形しないように注意します。
(6)乾燥
型から抜き取った成型物を乾燥させます。 乾燥工程は、原則天日干しと焙炉(ほいろ)乾燥の2段階です。 天候により天日干しが困難な場合は、焙炉乾燥のみとなります。 天日干しの期間は、小さい部品が2~3日間、大きい部品が4~5日間程度です。
焙炉乾燥する際は、手や体幹等の部品を金網の籠に入れます。 焙炉の下部で練炭を燃やして焙炉内の温度を上げて乾燥させます。 乾燥具合を確認するために、頃合いを見て木槌等で部品を叩いて音を聞いて確認します。
(7)バリ取り
十分乾燥したら、成型物の周囲についた不要なでっぱりのバリを削って取ります。 小刀で削り、細かいところは、サンドペーパーで磨きます。
(8)整形
バリ取りをした成型物を組立てます。 成型物には型と型の接着部分に隙間が生じます。 また、組立後に体の各部位の間に隙間が生じます。 整形工程では、この隙間を餅糊と石膏の混合物で埋めます。
(9)下塗り
膠(にかわ)に胡粉を溶かしたものを塗ります。 下塗りの場合、膠は板膠を用い、胡粉は牡蠣の殻から作られたものを用います。 湯煎で膠を液体にして胡粉を溶かします。 下塗りは、成型物を鍋に浸して付けます。 乾かす場合は串に刺した成型物を立てかけて置きます。 下塗りは4~5回行われますが、乾燥工程を挟みながら行います。
(10)上塗り
下塗り後、半年~1年間乾燥させた後に上塗り工程に入ります。 上塗りではクジラの膠と蛤の胡粉を用います。 上塗りは吹付けとハケで行います。 吹付けの後にハケを用いて仕上げます。
(11)仕上げ
上塗りが終わったら残すは仕上げです。 全体を磨いて、顔を描き髪の毛を付けます。 加賀友禅や古い布でつくった着物を着せ、獅子頭や纏等を持たせて人形は完成です。 人形の他、台座や屏風等を付属として付ける場合もあります。